BASF strengthens performance materials production in China
BASF has undertaken three key capacity expansion projects for performance materials at its Pudong site in Shanghai: Ultramid® (polyamide, PA), Ultradur® (polybutylene terephthalate, PBT), Elastollan® thermoplastics polyurethane elastomers (TPU), and Technical Center and capacity expansion of Cellasto®(microcellular polyurethane components).
“More than 60% of China’s people will live in cities by 2020. Supporting an environmentally-friendly path for urbanization presents a huge opportunity for chemistry as an enabler for sustainable innovations in areas ranging from industrial manufacturing to construction, transportation and consumer goods,” said Albert Heuser, President, Greater China and Functions Asia Pacific, BASF.
“As the leading producer of polyamide, PBT, TPU and Cellasto®, and preferred business partner for our customers , we continuously strengthen our position in key markets. With our technical and engineering competence, we help our customers differentiate in their market s and gain a competitive advantage. We put a strong emphasis on new market and product development, and these capacity expansions will support this future growth,” said Raimar Jahn, President, Performance Materials, BASF.
BASF’s biggest compounding facility in Asia Pacific for Ultramid® polyamide and Ultradur® PBT compounds starts operation ahead of schedule
BASF estimates the Asia Pacific market for engineering plastics will grow on average by about 7% per year. This growth is driven by the increasing usage of engineering plastics in various segments, including transportation, construction, high speedrailway, as well as the electrical and electronics industry. Ultramid® and Ultradur® are used in automotive parts and innovative applications include seat structures, oil sump modules, sensors, engine mounts, connectors and highly integrated laser-structured electronic devices.
Additionally, according to China’s national New Urbanization Plan (2014-2020), with additional 100 million people living in cities by 2020, the percentage of more energy-efficient and environmentally-friendly buildings among newly constructed buildings in China will rise to 50% from 2% today. BASF recently introduced co-extrudable Ultradur® to reinforce thermally insulated PVC window profiles, an important contributor to building energy efficiency.
The compounding plant’s total capacity for Ultramid® and Ultradur® compounds has doubled from currently 45,000 to more than 100,000 metric tons per year – making it BASF’ s biggest engineering plastics compounding facility in Asia Pacific. The expansion, which is operational more than six months ahead of schedule, also includes a compounding line for specialty grades that enables BASF to tap the burgeoning market potential for specialty applications. With this project and the new compounding plant in Yesan, Chung Nam Province, Korea, which is expected to begin operations from the end of 2015, BASF’s overall compounding capacities in Asia will increase from the current 130,000 to a total of 225,000 metric tons.
Significant increase in capacity of Elastollan® TPU reinforces BASF’s position in the region
Elastollan® TPU is a versatile material that offers the highest innovation potential. It can be processed with different methods, including extrusion and injection molding as well as blow molding.
BASF has now completed a significant capacity expansion at its Shanghai-based Elastollan® plant, which was established in 2007. Elastollan® TPU has a long history of success in China. The expansion of capacity for TPU in China will support growth of the rapidly growing market for textile, footwear, transportation, wire and cable sheathing and other industrial applications.
Technical and capacity enhancement of Cellasto® better serves the dynamic Asian automotive market
In 2013, more than 42 million cars were sold in Asia Pacific and over 20 million in China, the world’s largest automotive market. The number is foreseen to increase to 33 million in China and 62 million in Asia Pacific by 2020. (Source: LMC Automotive Ltd 2013 R eport).
Cellasto® is the customized solution for damping and reduction of the noise, vibration and harshness (NVH) level of vehicles. In Asia Pacific, BASF will strengthen the technical leadership of Cellasto®, based on the existing facilit y at BASF Pudong site, which was established in 2011 . The new investment project includes the expansion of the Cellasto® Asia Pacific Technical Center, the establishment of three new production lines , and the technical improvement of existing facilities. The production capacity will be doubled after the project completion in 2015.
BASF currently produces Cellasto® at six sites worldwide: Lemförde, Germany, Shanghai and Nansha, China, Guaratinguetá, Brazil, Shinshiro, Japan, and Wyandotte, USA.
Most read news
Organizations
Other news from the department manufacturing
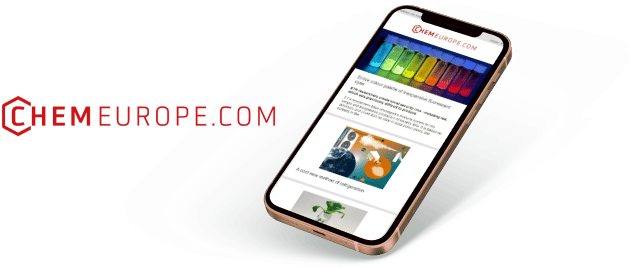
Get the chemical industry in your inbox
By submitting this form you agree that LUMITOS AG will send you the newsletter(s) selected above by email. Your data will not be passed on to third parties. Your data will be stored and processed in accordance with our data protection regulations. LUMITOS may contact you by email for the purpose of advertising or market and opinion surveys. You can revoke your consent at any time without giving reasons to LUMITOS AG, Ernst-Augustin-Str. 2, 12489 Berlin, Germany or by e-mail at revoke@lumitos.com with effect for the future. In addition, each email contains a link to unsubscribe from the corresponding newsletter.
Most read news
More news from our other portals
Last viewed contents
BASF opens new automotive coatings plant in Shanghai - State-of-the-art facility uses environmentally friendly production processes and technologies
AkzoNobel breaks ground on Decorative Paints site in China
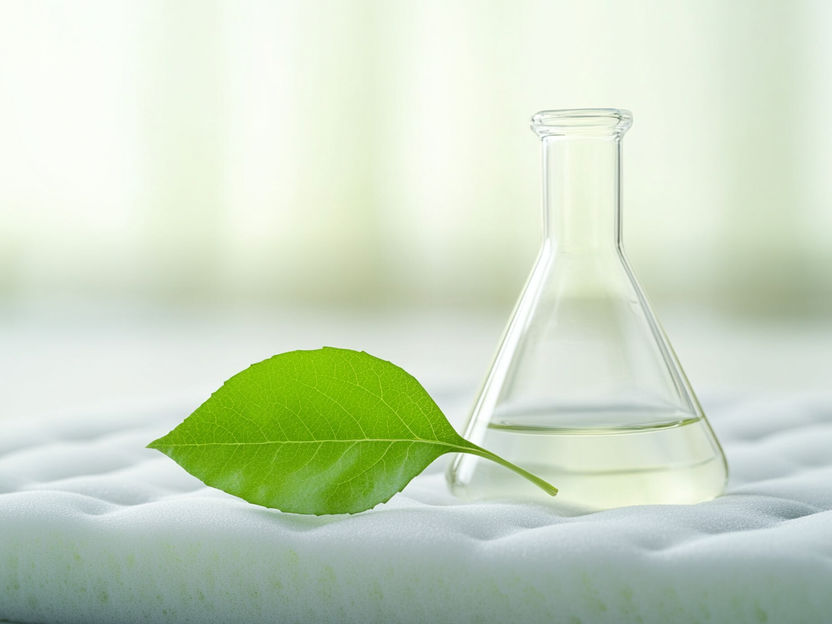
Cutting-edge technology for everyone - European innovation platform offers companies access to resource-saving production methods
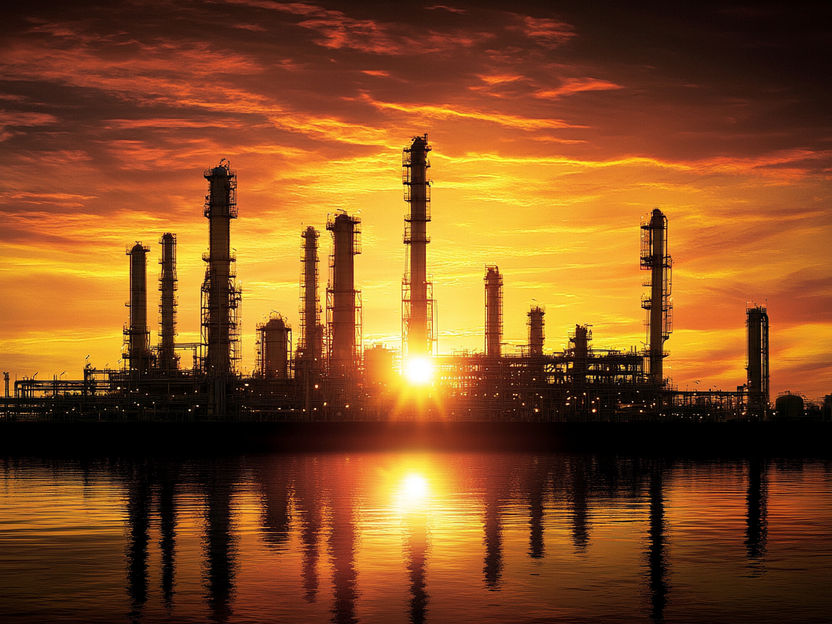
Arkema has decided to increase its PVDF capacity by 15% in North America
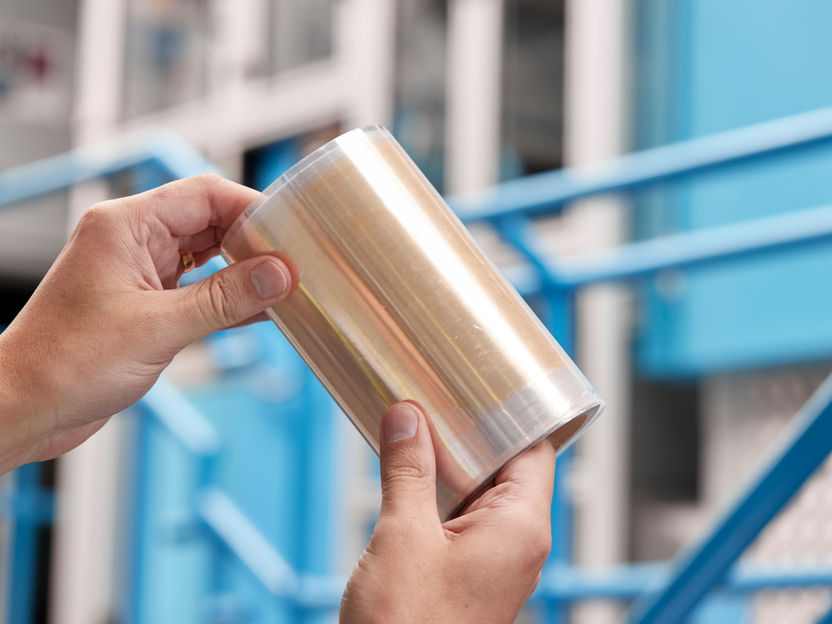
Green hydrogen economy: Evonik is building a plant for anion exchange membranes - Pilot plant for production of anion exchange membranes in Marl to start operation at the end of 2025
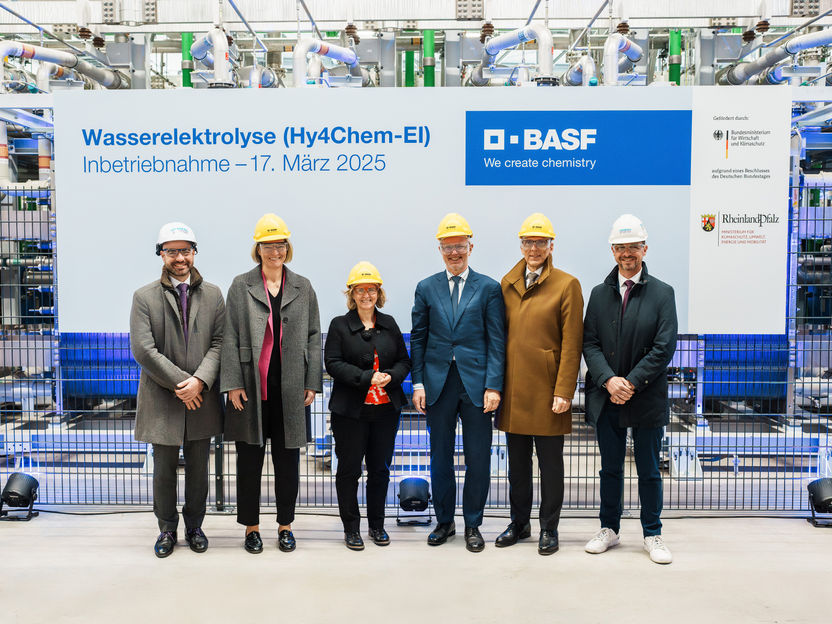
BASF commissions 54-megawatt water electrolyzer - Direct integration of the technology into a chemical production environment is a world first
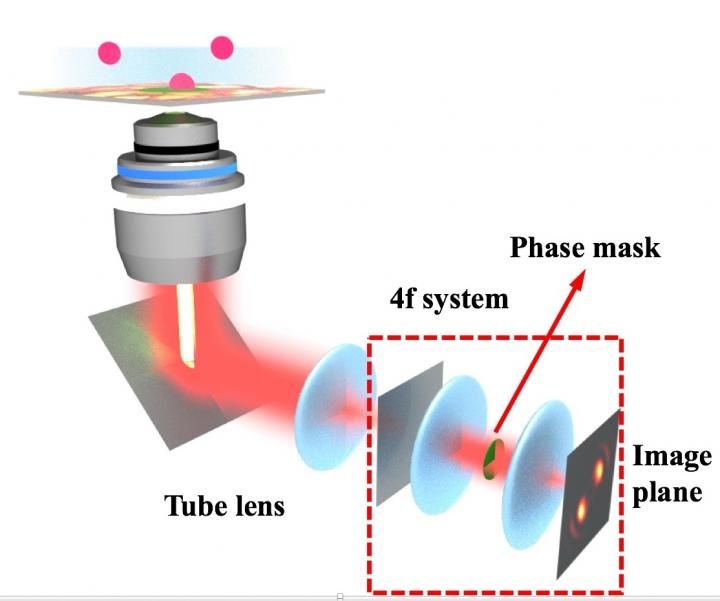
Shaping light lets 2D microscopes capture 4D data - Invention adds new dimension to fluorescent microscopy
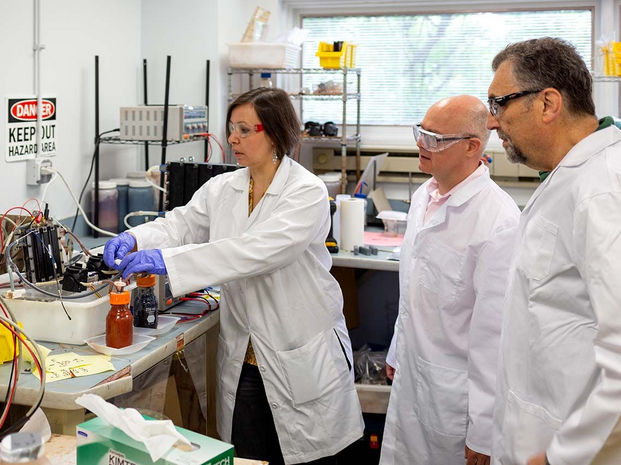
Illinois Tech ‘spinout’ startup Influit Energy has created the world’s first rechargeable, safe, electric fuel - “Discharged fluid can be returned to a recharge/refuel station for recharging or be charged inside the device by plugging into the power source”
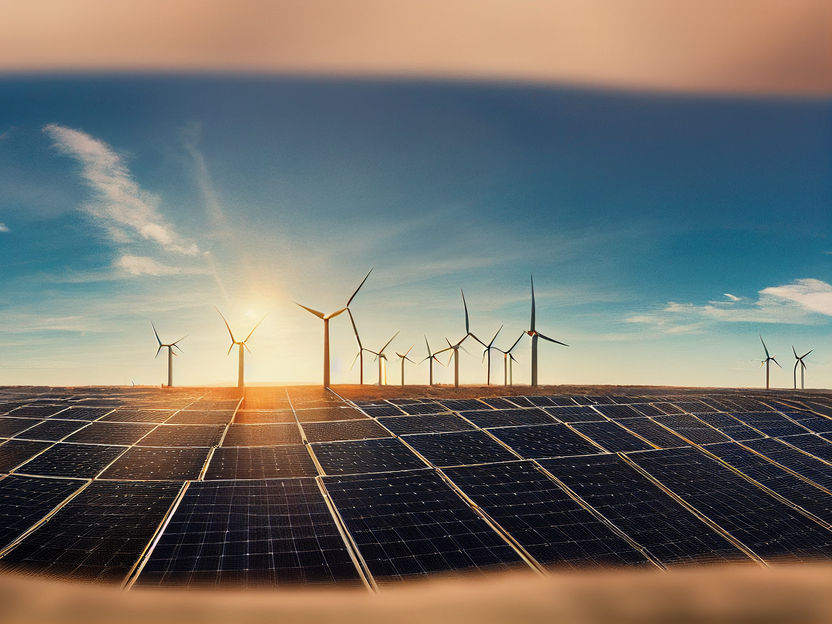
Clean-tech startup launches to create grid-scale battery infrastructure for greater use of wind and solar power - An innovative redox-flow battery
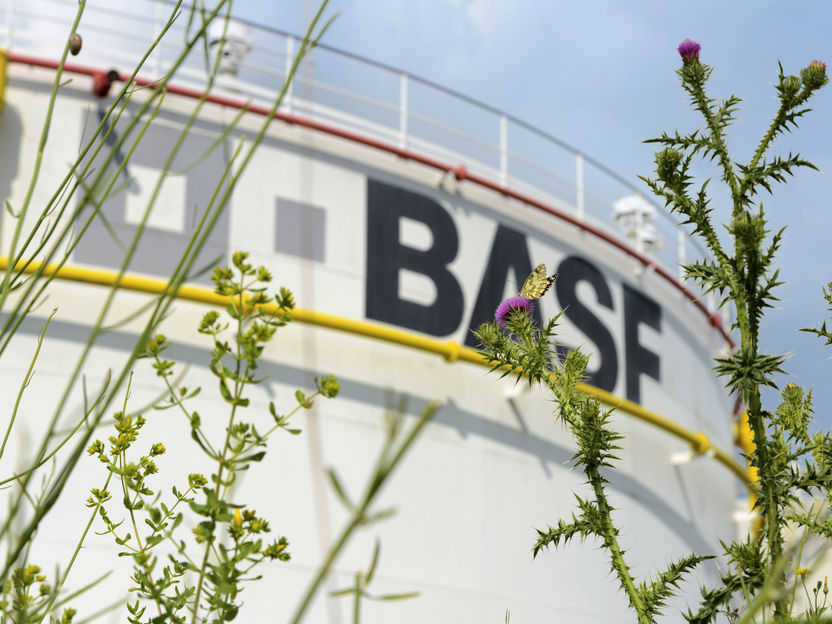
BASF’s Process Catalysts research team receives 2023 Edison Patent Award for novel adsorbent - Awarded BASF U.S. patent covers a novel method for reducing impurities in petrochemicals
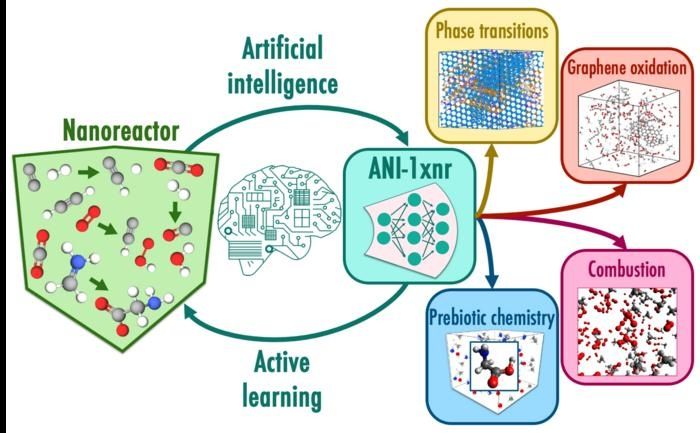
Artificial intelligence helps explore chemistry frontiers - Machine learning helps simulate reactive molecular dynamics for research and discovery
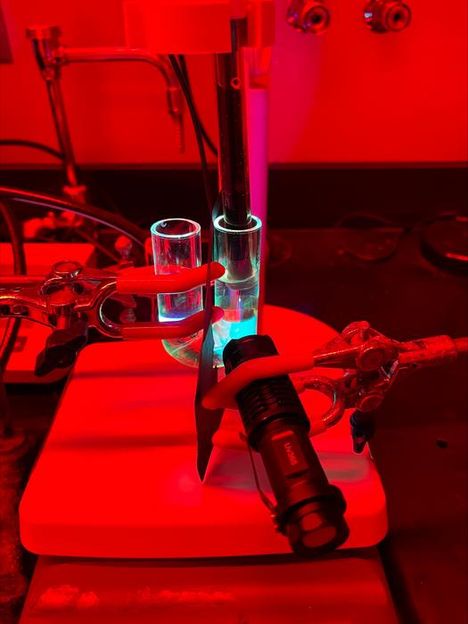