BASF commissions 54-megawatt water electrolyzer
Direct integration of the technology into a chemical production environment is a world first
Germany’s largest proton exchange membrane (PEM) electrolyzer has gone into operation at BASF’s Ludwigshafen site. Designed to produce zero-carbon hydrogen, the electrolyzer has a connected load of 54 megawatts and the capacity to supply the main plant with up to one metric ton of this substantial chemical feedstock every hour. After a construction period of around two years, the plant was officially inaugurated in the presence of the Rhineland-Palatinate State Minister for Climate Protection, Environment, Energy, and Mobility Katrin Eder, and Udo Philipp, State Secretary at the German Federal Ministry for Economic Affairs and Climate Action.
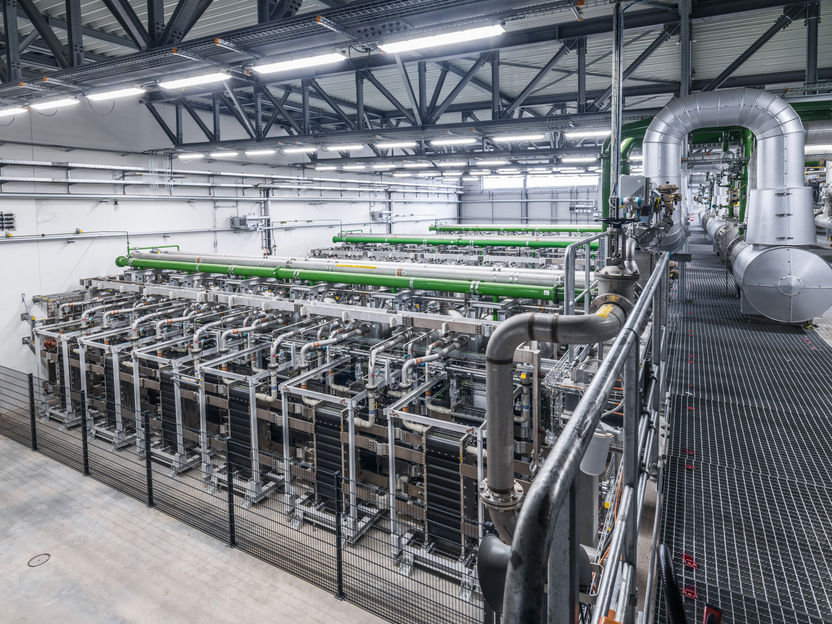
The individual electrolyzer modules are linked to each other and to the H2 network at the site in three so-called arrays.
BASF SE
Built in cooperation with Siemens Energy, the water electrolyzer is embedded in the production and infrastructure at the Ludwigshafen site, making it truly unique in terms of its interface and integration into a chemical production environment. A total of 72 stacks – modules in which the actual electrolysis process takes place – have been installed in the system. The electrolyzer has the potential to reduce greenhouse gas emissions at BASF’s main plant by up to 72,000 metric tons per year.
The emission-free production of hydrogen – using electricity from renewable sources – is fundamental to the market ramp-up of chemical products with a reduced carbon footprint. Once produced, the hydrogen is fed into the site’s hydrogen Verbund network and distributed to the production facilities as a raw material. In addition to using it as a feedstock for chemical products, BASF plans to supply hydrogen for mobility in the Rhine-Neckar Metropolitan Region, supporting the development of a hydrogen economy in the area.
In cooperation with the State of Rhineland-Palatinate, the German Federal Ministry for Economic Affairs and Climate Action provided funding of up to €124.3 million for the construction of the plant – €37.3 million of which was financed by the government of Rhineland-Palatinate. BASF’s investment in the project amounts to around €25 million. The project, entitled Hy4CHem, was selected as part of the IPCEI Hydrogen expression of interest procedure and subsequently funded as an individual project.
Katja Scharpwinkel, member of BASF SE’s Board of Executive Directors and Site Director Ludwigshafen, said: “The commissioning of the electrolyzer makes it possible for us to support our customers in achieving their climate targets by offering them products with a lower carbon footprint. At the same time, we are gaining experience at our largest Verbund site with the integration and operation of a system that brings us another step closer to transforming our main plant in Ludwigshafen. We welcome the fact that the federal government and state government have recognized the importance of this technology and provided us with significant support toward the project’s implementation.”
Alexander Schweitzer, Minister-President of Rhineland-Palatinate, commented: “The commissioning of the electrolyzer at BASF for the production of green hydrogen is a milestone for the ramp-up of the hydrogen economy in Rhineland-Palatinate, Germany, and Europe and an important commitment of BASF to its technology and production site in Ludwigshafen. With the Hy4Chem project, BASF is impressively demonstrating how the transformation of the energy-intensive chemical industry can succeed – innovatively, sustainably, and internationally competitively. As the state government, we support this process with up to €37.3 million because we are convinced that hydrogen plays a key role in decarbonizing and securing our industrial jobs. Today's inauguration sends a strong signal for a climate-neutral future and strengthens Ludwigshafen as a business location.”
Udo Philipp, State Secretary at the Federal Ministry for Economic Affairs and Climate Action, said: “I am delighted that the federal government’s efforts to support the hydrogen economy in Germany are bearing fruit. A flagship project for the integration of hydrogen into a chemical production site has become a reality at the Ludwigshafen site. It is the largest project of its kind in Germany to date, making it an important pioneer as we strive to achieve our climate targets. Through this collaboration, BASF is demonstrating what decarbonization of the industrial sector can look like in practice and inspiring further technological progress.”
Katrin Eder, Rhineland-Palatinate’s State Minister for Climate Protection, Environment, Energy, and Mobility, added: “BASF has embarked on an ambitious path to net zero. In addition to progressively increasing its generation of electricity and process heat from renewable energies, the company also plans to use renewable raw materials as alternatives to the fossil energy sources currently employed, such as natural gas. Designed to produce green hydrogen as a raw material, the new electrolyzer at the Ludwigshafen location represents an important milestone and supports the achievement of Rhineland-Palatinate’s climate protection targets.”
Among other applications, hydrogen is used in the production of ammonia, methanol, and vitamins. Until now, hydrogen has been produced at the Ludwigshafen location primarily by means of natural gas-based steam reforming or as a coupling product and by-product. With the electrolyzer, BASF is now taking an important step in the transformation of hydrogen production technology.