From Waste to Industrial Raw Materials
KIT Demonstrates Technologies for Circular Economy at Pilot Scale
With rising energy costs, dwindling resources, and growing volumes of trash, humanity has a waste problem. Researchers at the Karlsruhe Institute of Technology (KIT) have created a new development platform for a more sustainable circular economy: the Carbon Cycle Lab (CCLab). Their research includes a project for chemical recycling of plastic waste, which is being shifted to pilot scale. The project’s aim is to include previously non-recyclable waste in material cycles.
Global plastic production has increased significantly over the past 70 years, reaching about 414 million tonnes in 2023. However, the recycling rate is only 10 percent. Since energy costs are expected to continue rising while resources become scarcer, industrial transformation must include higher recycling rates. KIT is contributing to efforts to achieve higher rates with its new research platform, the Carbon Cycle Lab (CCLab). With their bioliq® project, KIT researchers had already developed a complete recycling process for biological residues. The CCLab now extends their work to the chemical recycling of plastic waste. “For a carbon-neutral circular economy, we need to return waste from industry, households, agriculture, and forestry to our material cycles, and we need to use renewable energy to do so,” said Professor Dieter Stapf, who heads KIT’s Institute for Technical Chemistry. A closed carbon cycle is better for the environment and conserves scarce resources, according to Stapf. “In our country, energy and resources are scarce and expensive,” he added. “In the future, our waste will be a raw material. Recycling it is efficient and economical and will help us reduce our dependency on fossil fuel imports, which has become especially urgent with the crisis in Ukraine."
The Carbon Cycle Lab Benefits from bioliq® Insights
KIT is already conducting extensive research on the use of biogenic residues and renewable resources to produce sustainable chemicals and fuels. In the bioliq® project, which was completed late last year, KIT scientists and their partners set up the first pilot plant capable of producing tonnes of gasoline from straw. “Much of what we have learned from bioliq® is going into CCLab,” said Professor Frederik Scheiff, head of the Fuel Technology Division at KIT’s Engler-Bunte Institute. “In the last operating campaign, we demonstrated a potential way forward by converting plastic pyrolysis oils to chemical raw materials for the first time. That was something nobody else had really done yet,” Scheiff said. “We’ve learned how to develop and scale such technologies, and we’ve showed that they can also be used to convert complex and previously non-recyclable plastic waste into chemical raw materials.”
Exploiting Previously Non-recyclable Waste
The new CCLab research platform is a logical continuation of the methods begun with bioliq® for recycling waste materials. High-quality recycling is impossible for most plastic products today because of their chemical composition and impurities. “We’re working in the CCLab on recycling materials that are still being burned or buried today, which causes greenhouse gas emissions,” Stapf said. Ultimately, the new technologies developed at KIT will enable the synthesis of new plastics from plastic waste without using oil or natural gas, and will separate or destroy the harmful substances and impurities in the waste. The resulting products will then undergo further processing to create raw materials for the production of new plastics. With the CCLab, the researchers aim to demonstrate the entire value chain. “The Carbon Cycle Lab is an important development platform for the sustainable circular economy. We’re shifting new technologies from research at KIT and in the Helmholtz Association to pilot scale,” Stapf said.
High Demand for Recycling
Such technologies are urgently needed; the EU’s recycling targets call for an additional 10 million tonnes of plastics to be recycled annually in Europe by 2035. For Germany, which produces a third of Europe’s plastics, that would mean another 2 to 3 million tonnes per year. “With the European Green Deal, the European Union plans to transition to a resource-efficient, carbon-neutral, and competitive economy. The CCLab is providing important insights into how that can work at an industrial scale,” Stapf said.
At KIT, the Institute of Catalysis Research and Technology, the Engler-Bunte Institute, and the Institute for Technical Chemistry are involved in the CCLab. In addition, there are technology transfer partnerships with numerous industrial companies. Since CCLab is part of the Helmholtz Association, it is funded by the German government.
Most read news
Topics
Organizations
Other news from the department science
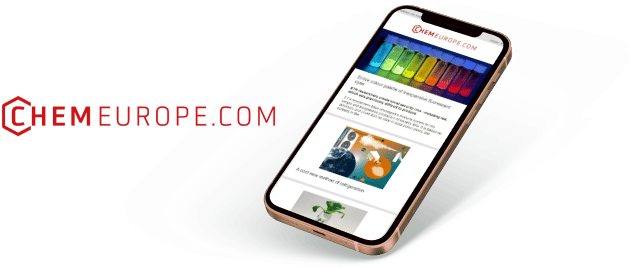
Get the chemical industry in your inbox
By submitting this form you agree that LUMITOS AG will send you the newsletter(s) selected above by email. Your data will not be passed on to third parties. Your data will be stored and processed in accordance with our data protection regulations. LUMITOS may contact you by email for the purpose of advertising or market and opinion surveys. You can revoke your consent at any time without giving reasons to LUMITOS AG, Ernst-Augustin-Str. 2, 12489 Berlin, Germany or by e-mail at revoke@lumitos.com with effect for the future. In addition, each email contains a link to unsubscribe from the corresponding newsletter.
Most read news
More news from our other portals
Last viewed contents
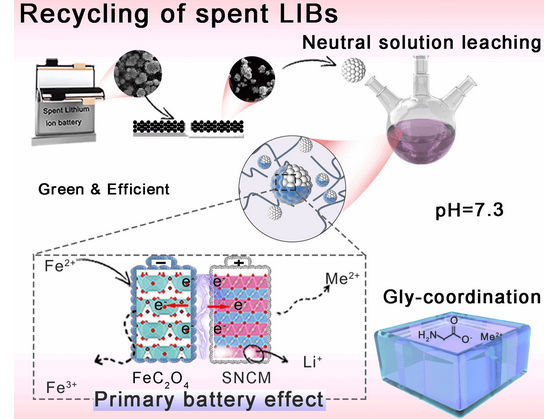
Amino Acid Assists in Recycling Rechargeable Batteries - Environmentally friendly and efficient: recycling lithium-ion batteries in neutral solution
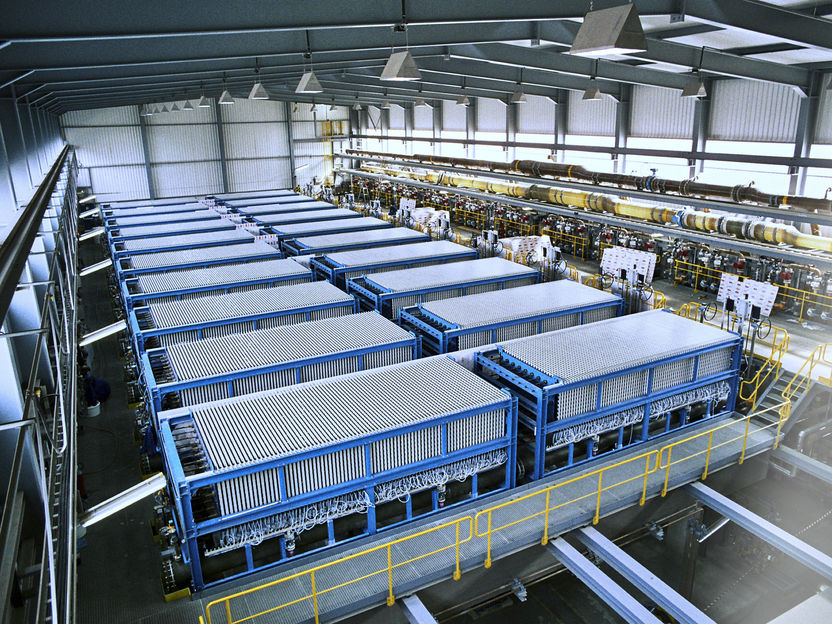
Air Products and thyssenkrupp Sign Exclusive Strategic Cooperation Agreement - World-Scale Electrolysis Plants to Generate Green Hydrogen
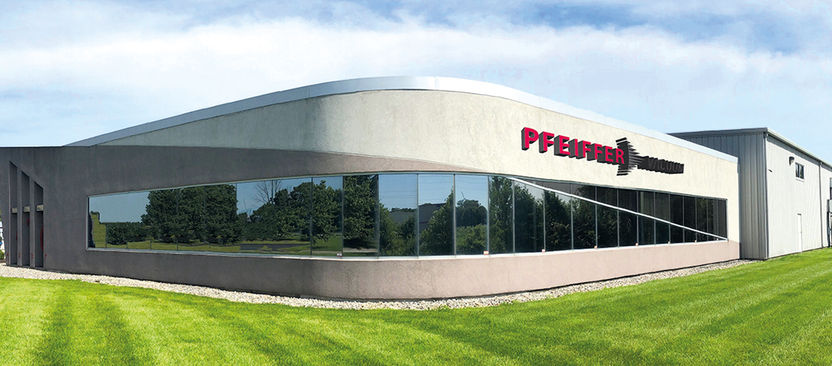
Pfeiffer Vacuum Opens New Leak Detection and Vacuum Technology Facility in Indianapolis, Indiana
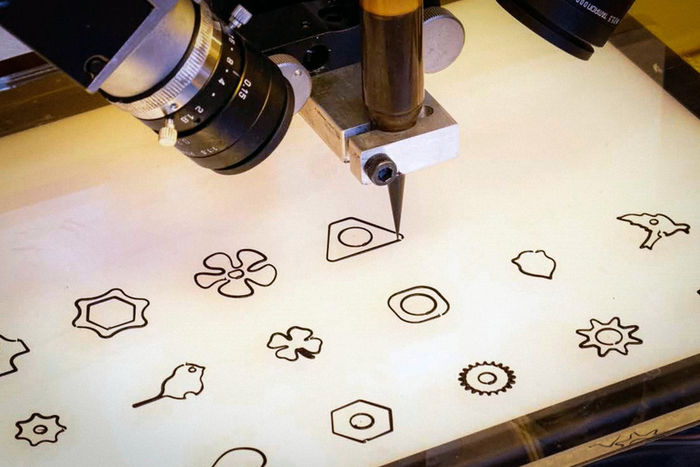
Using artificial intelligence to control digital manufacturing - Researchers train a machine-learning model to monitor and adjust the 3D printing process to correct errors in real-time
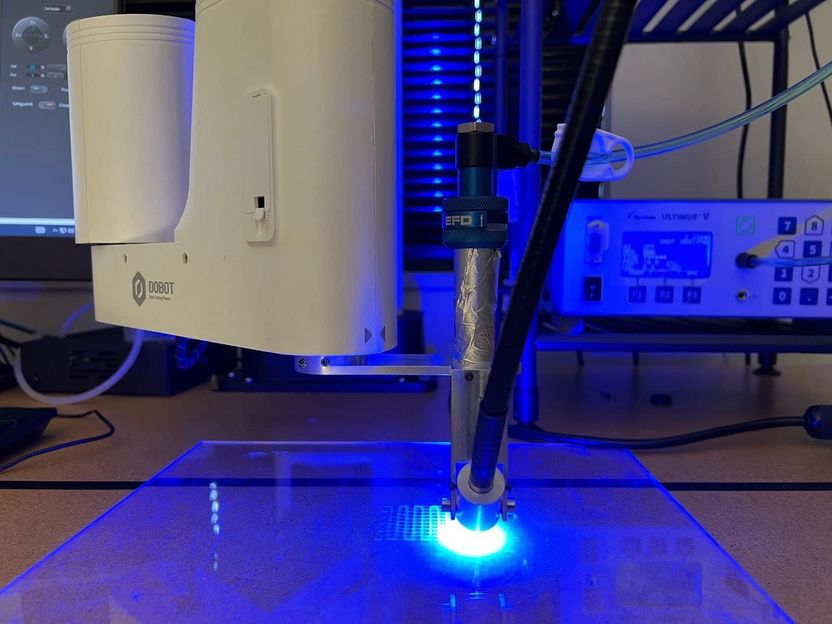
You can make carbon dioxide filters with a 3D printer
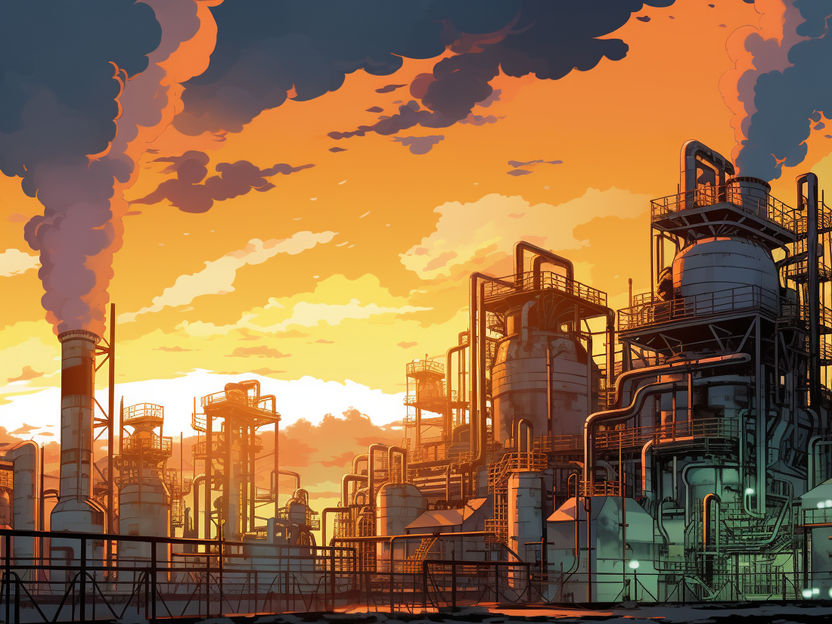
Carbon capture method plucks CO2 straight from the air - Using humidity-powered technology, researchers found several new ions that facilitate low-energy carbon sequestration
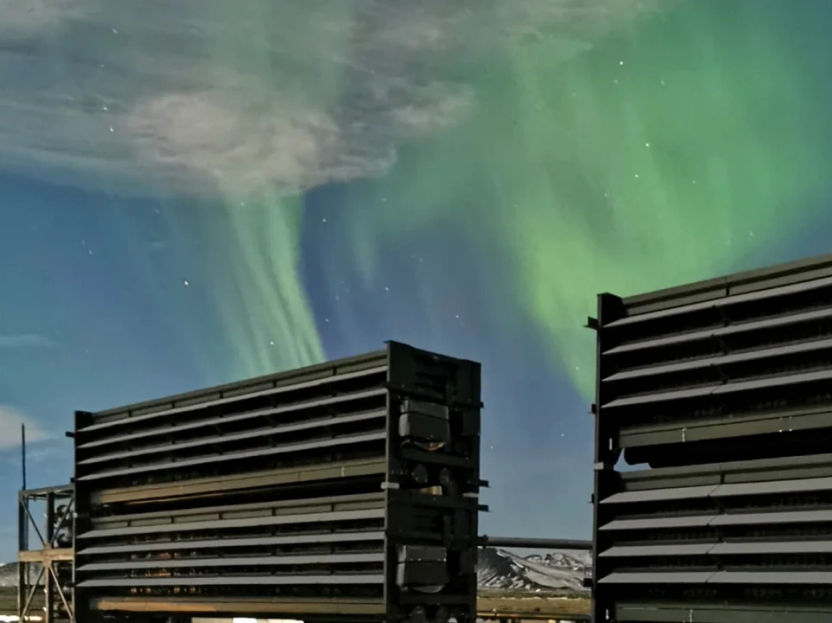
Climeworks and Svante collaborate in development and supply for direct air capture - Both companies agree to collaborate on three major CO₂ removal projects
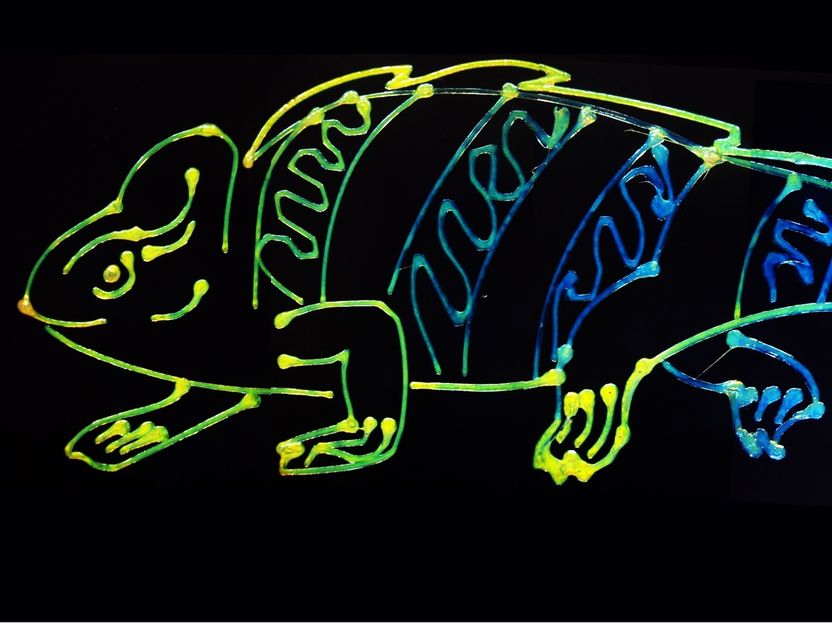
Chameleons inspire new multicolor 3D-printing technology - Researchers developed a sustainable technique to 3D print multiple dynamic colors from a single ink

Cost of direct air carbon capture to remain higher than hoped - Three technologies and their costs
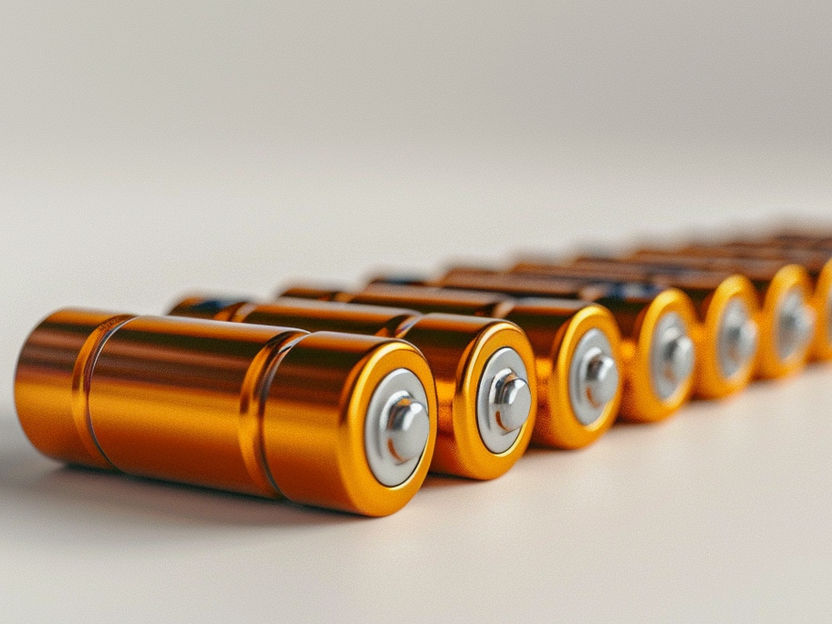
Improving battery production processes - EU project for efficient and sustainable European production of lithium-ion batteries
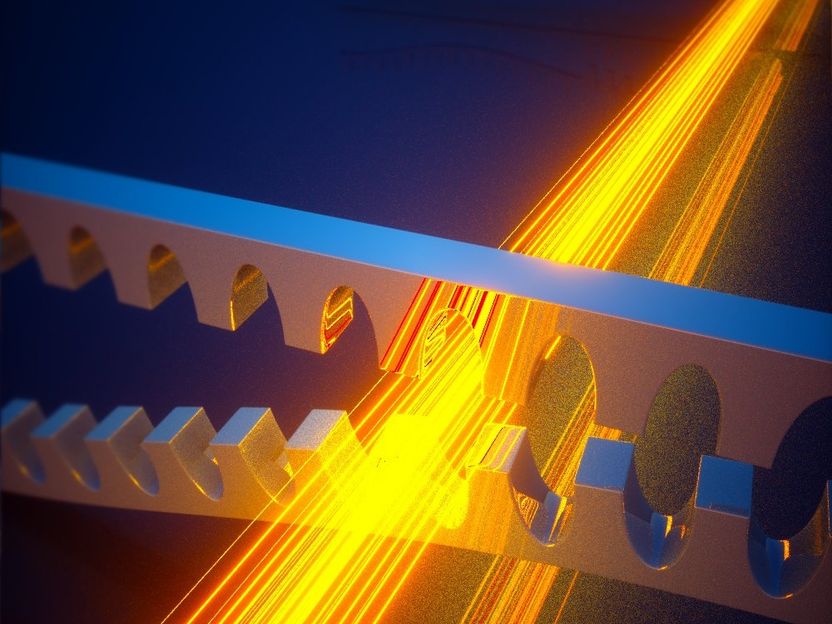
New topological metamaterial amplifies sound waves exponentially
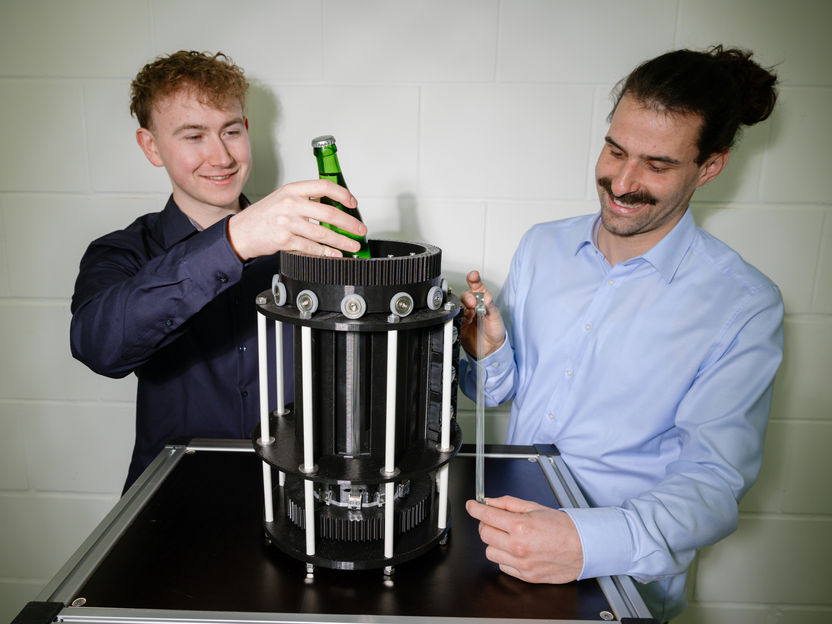